打造生产数据闭环,提高质量管控能力
当制造业遇上数字经济,驱动着传统产业加速变革成为必然,信息化也处于深刻的变革之中。德国工业4.0、美国工业互联网和中国这三大国家战略虽在表述上不一样,但本质上异曲同工,旨在智能制造。
在企业发展过程中始终坚持以信息化带动工业化、以工业化促进信息化,追求可持续发展模式。逐步推进智能制造新模式的建设,积极借助信息化时代的优势,导入智能制造模式,优化运行系统,提升设备生产制造能力,积极应对高效率、高质量、低成本方面的压力与挑战。
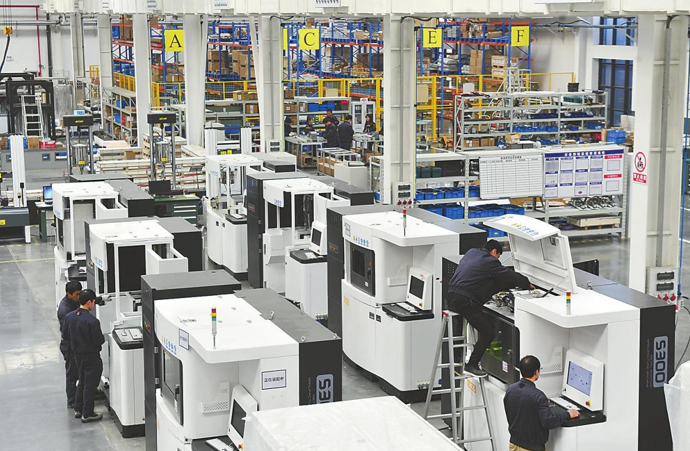
抓住发展变革的机遇,对企业的整个生产运作流程进行大幅度的改善,实现“效率要提升,成本要降低”的目标,由此开启的合作之旅,开始在信息化方面大量投入。
开启集团信息化的进程,正式启动APS项目,以此来满足客户的严苛要求。通过APS系统的建设,从而实现工单的精细化管控、物料批号、生产批号追溯等目标。
模具智能化管控,达到降本增效
在生产过程中,需要根据不同行业客户的不同生产需求,在生产过程中要进行频繁的换线、换模具。企业通过人工及看板管控的方式,将模具全部放在一个固定的位置,虽然也取得了一定的效果,但仍然存在寻找模具耗费时间长,从而影响换线及生产效率的状况。
在引入APS系统后,针对每一个模具,从上模到入库、出库,以及模具的保养等信息,都在系统里得到实时显示和统一管理,所有模具管理信息透明化。对数据的提取及分析有了极大的便利,同时也避免了通过手工报表的方式出现人为因素干扰,以及纸质信息不便保存等缺点。
另一项非常重要的工作是对原材料的追溯,从对供应商的选择到原材料入库后的库位管理、快速领料等工作有着极高的要求。引入信息化后,包括领料、入库、报价、报废等基础数据可以在ERP中直接提取出来,企业可以针对这些数据进行专业分析,避免了资源浪费、额外作业、管理不当,或材料丢失等问题,降低了相关费用,也保证了信息的安全性和信赖性。
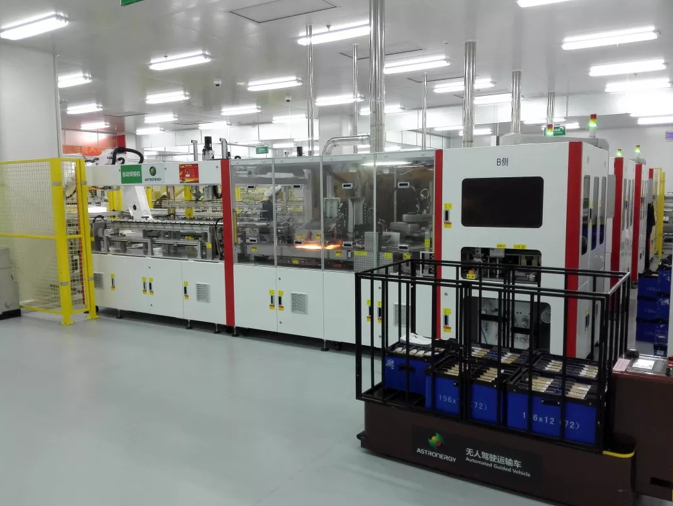
加强质检作业效率,品质管理更智动
引入APS系统,其原始数据取自ERP,从ERP渠道中与更多的因素进行关联,包括一些工单的信息、机台、作业人员、原物料的批次等等,形成一个管控网络,可以透过其中一个因素,追溯到跟它相关联的很多的因素。
在原来的工作中,需要冲压部的作业人员在测量室与冲压车间之间进行来回监测结果的确认动作,首件检查通过后才可以进行开工,经常造成大量的时间等待浪费。引入APS系统后,在测量室安装APS客户端,测量室的首件检查检测信息会实时反馈到冲压机台作业人员的工位电脑,避免了人员来回跑动和潜在的时间等待浪费。
此外,透过系统进行事前防堵,开工前系统管控机制设置,上料检查确保使用正确物料批次,并根据提前维护的设备点检表信息,在开始生产前在APS系统内做电子化设备点检,点检的效率得到提高的同时,完全解决了纸质点
检表单容易丢失和不利于保存的缺点。
生产的信息随时都在ERP跟APS系统间进行数据交互,基于对生产效率报表、模具维修履历报表、原材料追溯报表等这些数据的分析,了解生产内部的每一个环节是如何运转的,互相之间有没有衔接上,有没有出现浪费等问题,从而发现企业管理层面、生产环节中存在的一些漏洞,采取有针对性的一些措施。
从管理的角度来说,管理的实质无外乎是基于数字与事实的管理。如果我的管理脱离了这些因素,那生产运作的过程对我来说就像一个黑盒,只能看到表面,看不清楚里面具体怎么运作的的话,心里是没有底的。当企业的决策是基于数据、基于事实的,那企业的管理便会更加科学与合理。
布局智能工厂,智在数字未来
短期来说,因为APS系统的实施完成,企业会重点做一些报表的优化,使APS系统的功能得到全面的发挥,如对客制化报表的开发,从而为企业的有效决策提供一个很好的基础。
企业期望未来可以结合自动化改造,实现运营预警。能够看到每一个工位、工序的瓶颈在哪里,以此针对瓶颈做出改善,达到有针对性的提升效率。可以在智能制造系统中实现智能化管理,诸如分析、推理、判断、构思和决策等。
安达发是贴心的合作伙伴,项目只是开始,更会陪伴企业一起成长,提供定期的业务咨询和拜访服务,从容应对企业的业务增长和需求变化。
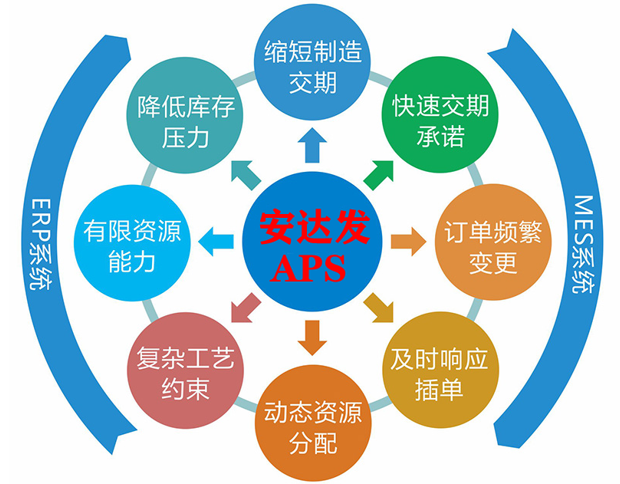
aps高级排程软件实现管理透明化,通过对生产流程和管理的不断规范和优化,使企业的管理水平不断提升,从而提高企业的服务水平和客户满意度,也为企业赢得良好的信誉和形象。
aps高级排程软件供应商能够成功,成长,壮大的基础也正是由于aps产品和服务具有高度的复制使用度,从而实现大规模交付。随着数字化转型的深水区到来,安达发在持续夯实自身技术的同时,聚焦行业核心需求场景,积极携手广大合作伙伴,打造可满足更多行业需求的场景化解决方案,助力制造业数字化转型,成就智能制造发展新动能,实现卓越制造。